Lauffähige und zuverlässige Maschinenbetriebszeiten sind die Basis für eine effiziente Prozess- und Produktionsgestaltung. Plötzliche Stillstände und spontane Maschinenwartungen verursachen erhebliche Kosten. Diese gilt es daher zu vermeiden. Aber wie lässt sich ein Maschinenausfall während der Betriebszeit erkennen? Welche Maschine fällt als nächstes aus und wann genau? Und welches Bauteil sollte als nächstes ausgetauscht werden und warum?
Predictive Maintenance liefert Antworten auf diese Fragen und noch viel mehr: Mithilfe von Predictive Maintenance lassen sich Störungen, Fehler und Ausfälle an Maschinen und Bauteilen vor ihrem Auftreten erkennen und dadurch Wartungen optimal planen. Doch was genau verbirgt sich hinter Predictive Maintenance und welche Vorteile entstehen dadurch? Wie gelingt die erfolgreiche Implementierung und welche Daten braucht es für die Umsetzung? Und wie genau kommt Machine Learning bei alledem zum Einsatz? All das erfahrt ihr hier.
Seitenverzeichnis
WAS IST PREDICTIVE MAINTENANCE UND WELCHE VORTEILE BRINGT DER EINSATZ?
Maschinenstillstände sind ein Albtraum für Unternehmen und mit erheblichen Kosten verbunden: So kann der einstündige Ausfall einer Maschine ein Unternehmen bis zu 220.000 EUR kosten. Hinzu kommt, dass die Ursachensuche für den Ausfall oftmals aufwendig ist und viel Zeit in Anspruch nimmt. Ziel ist es daher, Maschinenstillstände und insbesondere ungeplante Ausfälle bestmöglich zu vermeiden. Um das zu erreichen, ist es heutzutage gängig, Verschleißteile von Maschinen periodisch zu erneuern. Dahingegen erfolgt mit Predictive Maintenance die Inspektion oder Wartung dann, wenn tatsächlich notwendig (zustandsabhängige Wartung) und nicht nach starren routinemäßigen Intervallen (präventive Wartung) oder gar erst nachdem ein Defekt oder Ausfall eingetreten ist (reaktive Wartung).
Predictive Maintenance, die vorausschauende Wartung und Instandhaltung, beschreibt also die Fähigkeit, den Zustand einer Maschine jederzeit bewerten zu können und vorherzusagen, wie lange die Maschine den einwandfreien Betriebszustand noch beibehalten kann.
Die Vorteile liegen auf der Hand: Die Betriebszeit der Maschine wird maximiert, ungeplante Stillstände minimiert und die Wartungs- bzw. Servicekosten reduziert. Predictive Maintenance bringt aber noch viele weitere Vorteile, die bereits in zahlreichen Studien belegt wurden, so z. B. in der Studie „Predictive Maintenance: Service der Zukunft – und wo er wirklich steht“ vom VDMA und Roland Berger.
Die Vorteile entspringen dabei sowohl aus dem Bereich der Kostenreduktion als auch der Leistungssteigerung. Konkret lassen sich folgende Vorteile von Predictive Maintenance benennen:
erhöht die Anlagen- bzw. Maschinenverfügbarkeit
erhöht die Produkt- bzw. Prozessqualität
deckt die Ursachen für Störungen und Ausfälle auf
reduziert die Kosten für Wartung und Gewährleistung
minimiert Produktionsverluste
maximiert die Gesamtanlageneffektivität (GAE)
optimiert das Ersatzteilhandling
erhöht die Lebensdauer der Anlagen bzw. Maschinen
minimiert das Unfallrisiko
Aus diesen Gründen steckt für viele Unternehmen ein riesen Potential in der Erarbeitung von Predictive Maintenance. Und zwar entweder für die Maschinen in der eigenen Produktion oder für die beim Kunden eingesetzten Produkte. Doch wie genau funktioniert Predictive Maintenance?
WIE FUNKTIONIERT PREDICTIVE MAINTENANCE?
Ziel von Predictive Maintenance ist es, Machine Learning Algorithmen daraufhin zu trainieren, dass diese auf Basis von Maschinendaten und früheren Ausfällen, Muster erkennen, die Rückschlüsse auf einen drohen Ausfall zulassen. Diese trainierten Machine Learning Algorithmen können dann verwendet werden, um zukünftige Ausfälle oder Fehlerbilder und damit den bestmöglichen Wartungszeitpunkt vorherzusagen. Mit Predictive Maintenance wisst ihr also, wann und mit welcher Wahrscheinlichkeit eine noch im Betrieb befindliche Maschine ausfallen wird und warum. Wie das im Detail funktioniert, veranschaulicht folgende Übersicht:
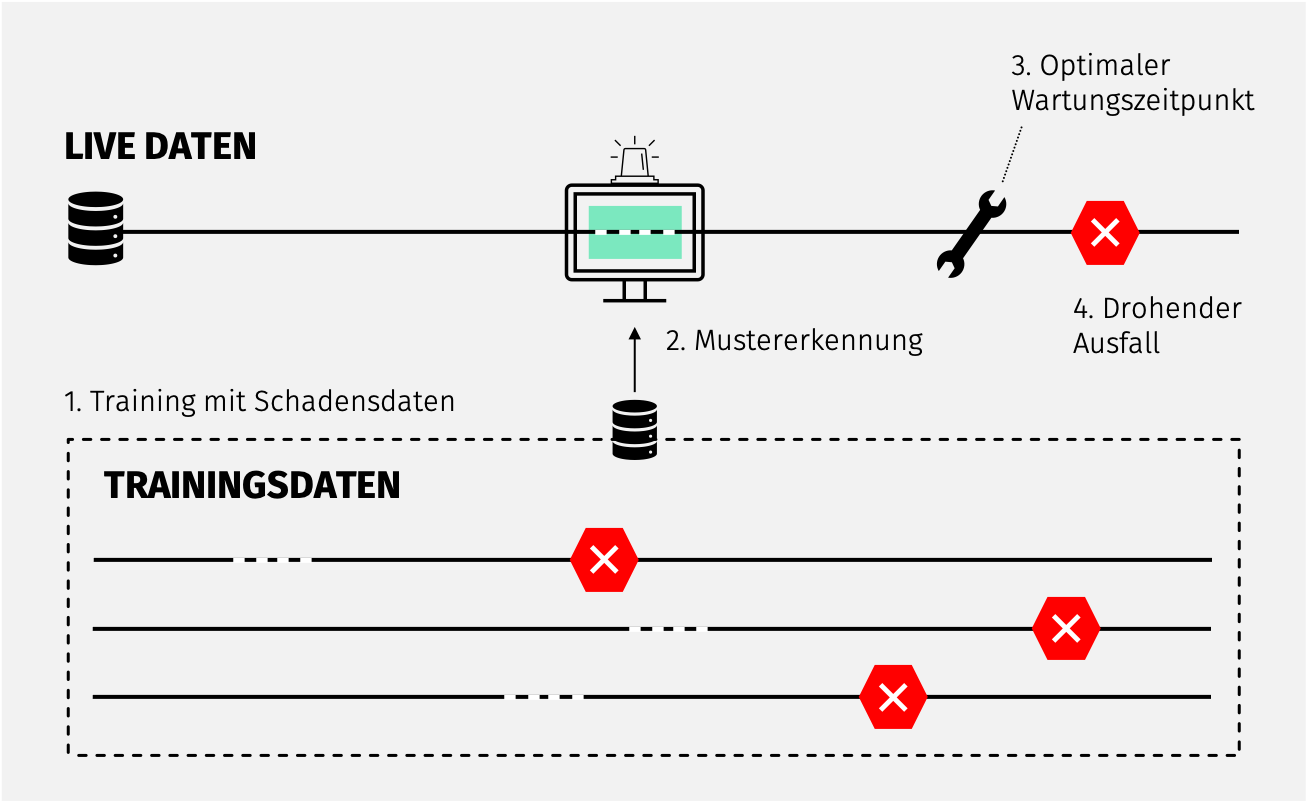
Predictive Maintenance lernt von früheren Maschinenausfällen, den optimalen Wartungszeitpunkt vorherzusagen
1. Training
Ein Machine Learning Algorithmus wird mit Daten aus früheren Ausfällen trainiert.
2. MUSTERERKENNUNG
Der Algorithmus gleicht die Live Daten mit den Trainingsdaten ab und erkennt Muster.
3. Wartungszeitpunkt
Durch die historischen Trainigsdaten lässt sich nun der optimale Wartungszeitpunkt vorhersagen.
4. Ausfall
Der Ausfall der Maschine kann durch die Mustererkennung frühzeitig verhindert werden.
Damit dies gelingt, müssen den Algorithmen also möglichst viele Beispiele von „gesunden“ Maschinen und Maschinen kurz vor dem Ausfall bereitgestellt werden. Auf dieser Basis lassen sich dann Ausfallprofile erstellen, die zwischen gesunden und fehlerhaften Maschinen unterscheiden können. Predictive Maintenance benötigt also eine umfangreiche Datengrundlage, die, sofern sie noch nicht besteht, aufgebaut werden muss. Doch welche Daten braucht es wirklich? Und wie und wo können diese Daten vorliegen?
WELCHE DATEN BRAUCHT ES FÜR PREDICTIVE MAINTENANCE?
Um Ausfälle oder Fehler anhand der Maschinendaten vorhersagen zu können, werden zwei verschiedene Datenquellen benötigt: Und zwar Maschinendaten und Informationen zu Ausfällen oder Fehlerbildern.
1. Maschinendaten
Unter Maschinendaten werden all jene Daten zusammengefasst, die im Betrieb von einer Maschine selbst gesendet oder die durch Sensoren außerhalb der Maschine erfasst werden. Dazu gehören neben den Maschinenstammdaten, Sensordaten und Fehlermeldungen, Prozesszustände und andere Qualitätskennzahlen. Diese Daten werden zum einen für das Training der Algorithmen benötigt, um Ausfallmustern zu erlernen und zum anderen für die anschließende Echtzeitüberwachung.
Gerade bei der Mustersuche haben Machine Learning Algorithmen einen entscheidenden Vorteil gegenüber uns Menschen. Denn wir Menschen stoßen bei der Vielzahl an Kombinationsmöglichkeiten, welche sich durch komplexe Ausstattungsvarianten, Baujahr, Zuliefererchargen, Einsatzbedingungen und so weiter ergeben, schlichtweg an unsere Grenzen und sind nicht in der Lage, die Einflussfaktoren zu identifizieren, die auf einen Ausfall hindeuten.
2. Schadensdaten
Unter Schadensdaten werden die Daten verstanden, welche die Maschinenausfälle oder Fehlerbilder beschreiben. Umso mehr Szenarien als Schadensdaten vorliegen, umso besser lassen sich Fehlerszenarien vorhersagen. Diese werden in der Regel durch Qualitätskontrollen im Werk, Reparaturmeldungen aus Werkstätten oder Garantieanträge erzeugt.
Um die Machine Learning Algorithmen trainieren zu können, müssen diese beiden Datenquellen miteinander kombiniert werden. Dies gelingt in der Regel über die Seriennummer oder die Betriebsstunde. Sind die Daten kombiniert, kann der Machine Learning Algorithmus sodann relevante Muster erkennen und letztlich Ausfälle vorhersagen. So können Wartungsaktionen frühzeitig geplant und Verschleiß und Schäden dann behoben werden, wenn es zeit-, kosten- und produktionsmäßig am vorteilhaftesten ist.
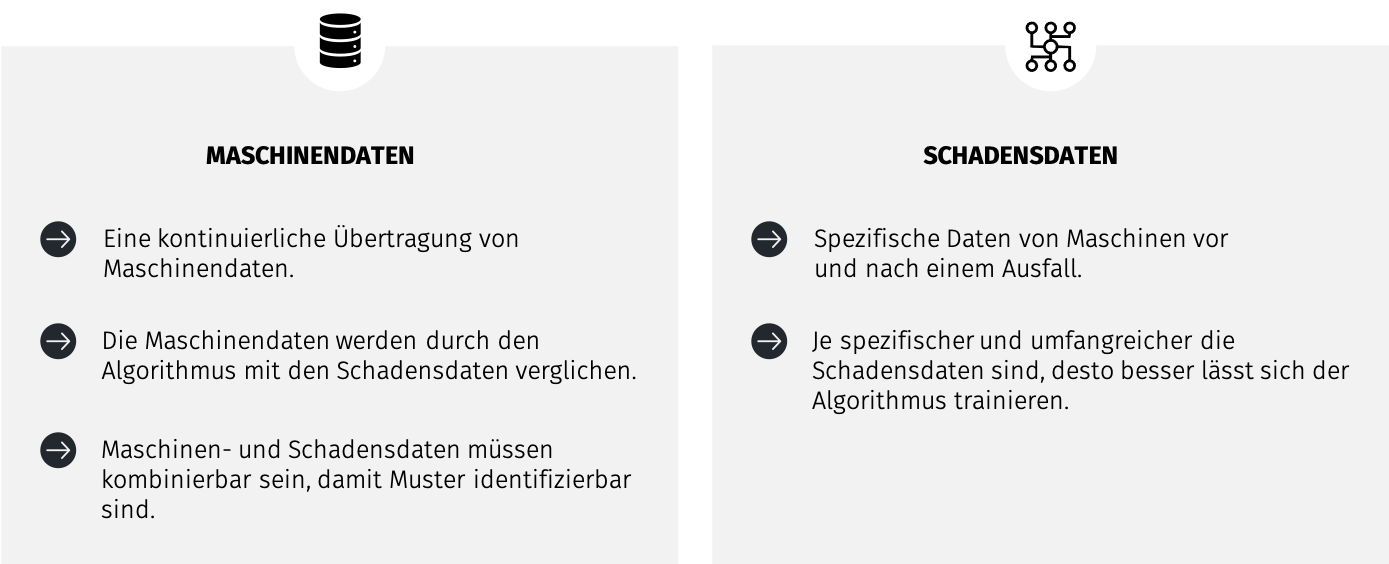
Ein Überblick über die für Predictive Maintenance benötigte Datengrundlage
FÜR WELCHE UNTERNEHMEN LOHNT SICH PREDICTIVE MAINTENANCE?
Predictive Maintenance ist eines der größten Einsatzfelder von Data Science im Kontext von Industrie 4.0. Von den Vorteilen einer vorausschauenden Wartung profitiert aber nicht nur das produzierende Gewerbe. Der Einsatz von Predictive Maintenance lohnt sich überall dort, wo teure und komplexe Maschinen quasi rund um die Uhr im Einsatz sind und unvorhergesehene Ausfälle und Stillstandzeiten zu hohen Kosten führen.
Zu den Branchen, die besonders für Predictive Maintenance Lösungen prädestiniert sind, gehören u.a. der Maschinen- und Anlagenbau, die Medizin- und Elektrotechnik, die Luft-, Raumfahrt- und Automobilindustrie, aber auch die Chemie- und Pharmaindustrie und nicht zuletzt auch der Bereich der Logistik und des Transportwesens, um nur einige Beispiele zu nennen.
FAZIT
Predictive Maintenance verspricht enorme Mehrwerte für Unternehmen. Damit ihr mit Predictive Maintenance durchstarten könnt, ist es wichtig, folgendes zu verstehen:
Predictive Maintenance benötigt eine umfangreiche Datengrundlage, die, sofern sie noch nicht besteht, aufgebaut werden muss.
Der Aufbau von Predictive Maintenance ist nicht zu unterschätzen. Es ergeben sich allerdings viele direkte Mehrwerte auf dem Weg zu einer vollumfänglichen Predictive Maintenance Lösung. Bei entsprechender Planung lassen sich erste Use Cases bereits beim Aufbau der Datengrundlage implementieren.
Egal wie es um Eure Predictive Maintenance Readiness steht, unser Data Activation & Innovation Team unterstützt Euch bei Eurem Vorhaben und berät Euch als Partner auf dem Weg.